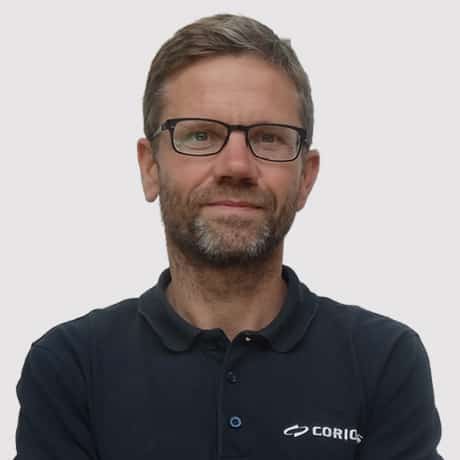
3 preguntas para Alexandre Hamlyn, cofundador de Coriolis Composites
Comenzando desde una Start-up, hasta convertirse en una PYME industrial, el recorrido de Coriolis Composites es admirable. La empresa especializada en la fabricación de células robotizadas y de programas informáticos para la fabricación de partes fabricadas en composites, emplea hoy a 170 personas y se impone en el mercado del Control no destructivo (CND).
Fundada el año 2000, en la ciudad de Lyon, por dos ingenieros, Clémentine Gallet y Alexandre Hamlyn, a los que luego se unió Yvan Hardy, Coriolis Composites se ha establecido desde entonces en Quéven, cerca de Lorient, con la ambición de automatizar los sistemas de fabricación destinados al sector náutico. Sin embargo, es el encuentro con la aeronáutica, lo que catapulta a Coriolis hacia el mercado de cabezales de colocación de fibra de carbono listos, destinados a prestigiosos clientes. Airbus, Stelia Aerospace, Dassault Aviation, Safran o la china Comac han posicionado a Quéven en el mapa de la aeronáutica mundial.
En 2011, Coriolis adquirió una cabina de prueba no destructiva diseñada y construida por Lemer Pax. Basándose en varios años de investigación e innovación, las dos empresas se unieron en 2016 para una colaboración sin precedentes: el diseño de una plataforma robótica de tomografía de rayos X de gran tamaño, que incorpora una cabina de protección radiológica de 70 toneladas para la CEA Tech..
¿Cómo comenzo la aventura de Coriolis Composites?
Alexandre Hamlyn : Todos salimos de la escuela de ingeniería y nos apasionaba la navegación. Deseábamos revolucionar la construcción naval, en la cual los obreros de los astilleros trabajan todavía con la fibra en grandes moldes, para luego pegarla a mano con resina. Hacer los cascos para los veleros de competencia en composites de forma industrial y no artesanalmente era el objetivo de nuestro pequeño equipo. El proceso de bobinado de filamentos utilizado en la fabricación de cañas de pescar o tanques, demostró ser adaptable a este nuevo desafío. la carrera de obstáculos comenzó entonces. Visitamos a todas las sociedades de inversión de capital de riesgo en Francia, participamos en los concursos organizados por el Ministerio de Investigación e Innovación y los ganamos todos uno tras otro. Nos entrevistamos con mucha gente. Fabricantes de carbono, socios potenciales e industriales para finalmente obtener el apoyo de Jean-Yves Le Drian, entonces diputado y Consejero Regional de Bretaña, y del fondo de desarrollo económico local, la condición impuesta fue instalarnos en Morbihan. Esto fue muy meritorio, pues en ese momento la industria no tenía suficiente soporte comunicacional, lo único que funcionaba era la Internet. Pero a pesar de estar entusiasmados, nunca conseguimos ningún cliente en el mundo de la navegación, rápidamente nos dimos cuenta que este sector no era el adecuado para nuestro proyecto. Las grandes unidades de competición se fabrican por unidad, lo que no es compatible con procesos robotizados y los barcos producidos en serie se fabrican con fibras de bajo costo. ¡No habia lugar para nuestra tecnología de fabricación automática!
Realizar los cascos de los veleros de competencia en composites de forma industrial y no artesanalmente, era por tanto el objetivo de nuestro pequeño equipo.
¿Cómo fue el despegue de la empresa?
Alexandre Hamlyn : Mientras tanto, desarrollamos la técnica del embobinado de filamentos inspirada en una tecnología americana para la defensa. Una tecnología costosa que ha sido adaptada en robots estándar para hacerlos articular de diversas maneras y obtener máquinas flexibles de robots antes lentos y difíciles de adaptar. Según el viejo adagio que dice: muchas ideas no compensan la falta de dinero, adaptamos esta tecnología robótica para controlar los costos de producción, mientras que al mismo tiempo Boeing lanzaba su avión fabricado en composites, especialmente piezas como las alas de 40 m hechas de ese material. Efectivamente, el primer impulso industrial vino del sector aeronáutico. En 2007, Airbus siguió el ejemplo y nos encargó una primer aparato. De una start-up de investigación y desarrollo, nos convertimos en una PYME industrial dedicada a satisfacer a los principales clientes del sector, preservando al mismo tiempo el ADN de Coriolis, gracias principalmente a ingenieros expertos en materiales, robótica y software. Nuestra empresa no realiza una actividad mecánica propiamente dicha, todas las piezas son encargadas a subcontratistas y nos llegan prefabricadas.
Efectivamente, el primer impulso industrial vino de la industria aeronáutica.
© Coriolis Composites
¿Cómo ves el futuro cercano de Coriolis?
Alexandre Hamlyn : Claramente en la diversificación. Acabamos de adquirir una empresa para la fabricación de tanques para vehículos impulsados por hidrógeno. Crecimiento externo, pero permaneciendo especializados en nuestra área de conocimientos de la robótica y los composites, integrando al mismo tiempo los temas de iluminación y ahorro de energía. Queremos limitar nuestra dependencia de la industria aeronáutica con el objeto de ganar nuevos mercados en los sectores automovilístico y naval, produciendo, por ejemplo, láminas compuestas para los grandes barcos de competencia. Al fabricar con una tecnología de colocación automatizada, que permite producir un panel de fuselaje de muy alta calidad en 3 horas, estamos desplegando en paralelo herramientas de ultrasonido y de rayos X destinadas a realizar inspecciones automatizadas de las piezas de composites. Hemos iniciado un proyecto con la CEA para una nueva tecnología de radiografía en 3D. Les suministramos los robots y el software y la CEA desarrolla todo lo concerniente a la reconstrucción de la imagen. Por último, el sector médico puede abrirnos otra posibilidad de crecimiento, con la confección de férulas de carbono por encargo. Coriolis Composites obtiene el 80% de sus ganancias, es decir 30 millones, a través de sus exportaciones, apoyándose siempre en una ambiciosa política de propiedad intelectual.
Paralelamente, estamos desplegando herramientas de rayos X ultrasónicas para la inspección automatizada de piezas producidas en composites.