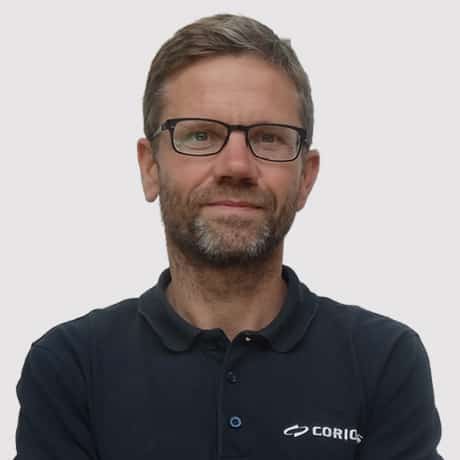
3 questions à Alexandre Hamlyn, co-fondateur de Coriolis Composites
De la Start-up à la PME industrielle, le parcours de Coriolis Composites est remarquable. L’entreprise, spécialisée dans la fabrication de cellules robotisées et de logiciels pour la production de pièces en composites, emploie aujourd’hui 170 personnes et se place sur le marché du Contrôle Non-Destructif (CND).
Fondé en 2000, à Lyon, par deux ingénieurs, Clémentine Gallet et Alexandre Hamlyn, rejoint par la suite par Yvan Hardy, Coriolis Composites s’est installé depuis à Quéven, près de Lorient, avec pour ambition l’automatisation des systèmes de fabrication, destinée à la filière nautique. À l’usage, c’est pourtant la rencontre avec l’aéronautique qui catapulte Coriolis vers le marché des têtes de placement de fibres de carbone avec de prestigieux clients à la clé. Airbus, Stelia Aerospace, Dassault Aviation, Safran ou le chinois Comac ont placé Quéven sur la carte de l’aéronautique mondiale.
En 2011, Coriolis s’équipe d’une cabine de contrôle non-destructif conçue et réalisée par Lemer Pax. Forts de plusieurs années de recherche et d’innovation, les deux sociétés se retrouvent en 2016 pour une collaboration inédite : la conception d’une très grande plateforme tomographie X robotisée intégrant une cabine de radioprotection pesant 70 tonnes pour le compte du CEA Tech.
Comment est née l’aventure de Coriolis Composites?
Alexandre Hamlyn : Nous sortions tous d’une école d’ingénieurs et étions passionnés de voile. Nous voulions révolutionner la construction navale où les ouvriers des chantiers travaillaient encore la fibre dans de grands moules pour l’encoller à la main avec de la résine. Réaliser des coques de voiliers de compétition en composites de façon industrielle, et non plus artisanale, était donc l’objectif de notre petite équipe. Le procédé de l’enroulement filamentaire, utilisé dans la fabrication des cannes à pêche ou des réservoirs, s’avérait adaptable à ce nouveau challenge. Le parcours du combattant pouvait alors commencer. Toutes les sociétés d’investissement en capital risque de France ont été démarchées, nous avons participé aux concours organisés par le Ministère de la Recherche et de l’Innovation et nous les avons tous gagné les uns après les autres. Nous avons croisé beaucoup de monde. Des fabricants de carbone, de potentiels partenaires, des industriels, pour être enfin soutenus par Jean-Yves Le Drian, alors député et conseiller régional de Bretagne, et son fonds local de développement économique. À la condition de venir s’implanter dans le Morbihan. C’était d’autant plus méritoire, de sa part, car à l’époque, l’industrie n’avait pas bonne presse. Il n’y en avait que pour le Net. Nous, en revanche, nous étions enthousiastes mais nous n’avons jamais décroché de clients dans le monde du nautisme ! On s’est vite aperçu que cette filière n’était pas calibrée à notre projet. Les grandes unités de compétition sont fabriquées à l’unité et n’ont donc pas besoin de robotisation et les bateaux de grande série sont produits avec des fibres à bas coût. Pas de place pour notre technologie automatisée de dépose !
Réaliser des coques de voiliers de compétition en composites de façon industrielle, et non plus artisanale, était donc l’objectif de notre petite équipe.
Comment s’est passé le décollage de la société ?
Alexandre Hamlyn : Entre-temps nous avons fait évoluer la technique de l’enroulement filamentaire en s’inspirant d’une technologie américaine développée pour la défense. Une technologie chère que l’on a adaptée sur des robots standards pour les rendre polyarticulés et obtenir des machines flexibles sur des robots lents et peu adaptables. Selon le bon vieux principe qui veut que l’on compense le manque d’argent par des idées à foison, nous avons adapté cette technologie robotisée pour maîtriser les coûts de production, lorsque Boeing sort, simultanément, son avion en composites. Avec notamment des pièces comme des ailes de 40 m de long en composites. C’est effectivement de l’industrie aéronautique qu’est venu le premier coup de pouce industriel. En 2007, Airbus emboîte le pas et nous a commandé une première machine. Nous sommes passés de la start-up de recherche et développement à la phase de production pour côtoyer les grands donneurs d’ordre de la profession, tout en préservant l’ADN de Coriolis autour principalement d’ingénieurs experts dans les matériaux, la robotique et les logiciels. En effet, il n’y pas de mécanique proprement dite chez nous, car tous les composants sont sous-traités et arrivent chez nous pré-assemblés.
C’est effectivement de l’industrie aéronautique qu’est venu le premier coup de pouce industriel.
© Coriolis Composites
Comment voyez-vous l’avenir proche de Coriolis ?
Alexandre Hamlyn : Il est clairement dans la diversification. Nous venons d’acheter une entreprise pour réaliser des réservoirs destinés aux véhicules à hydrogène. De la croissance externe donc, mais en restant spécialisé dans notre savoir-faire du robot et du composite tout en y intégrant les thématiques d’allègement et d’économie d’énergie. Il s’agit de contenir notre dépendance à l’aéronautique pour capter de nouveaux marchés dans l’automobile et le nautisme, en réalisant par exemple, des foils en composite pour les grands bateaux de course. Comme nous fabriquons de la technologie automatisée de dépose, qui peut en 3 heures réaliser un panneau de fuselage de très haute qualité, nous déployons, en parallèle, des outils de contrôles automatisés de pièces en composites ultrason rayons X. Nous avons engagé un projet avec le CEA pour une nouvelle technologie de radiographie en 3D. Nous leur livrons des robots et des logiciels et le CEA développe toute la partie reconstitution d’image. Enfin, le médical peut nous ouvrir une autre voie de croissance en proposant des orthèses en carbone sur commandes personnalisés. Coriolis composites réalise 80% de son chiffre d’affaires, soit 30 Millions, à l’export, en s’appuyant toujours sur une ambitieuse politique de propriété intellectuelle.
Nous déployons, en parallèle, des outils de contrôles automatisés de pièces en composites ultrason rayons X.